Analysis of the Working Principle and Application Scenarios of Radar Level Sensor
In the era of booming industrial automation and intelligent manufacturing, level measurement technology, as a crucial part of the industrial production process, has always occupied a key position. According to the latest report released by MarketsandMarkets, the global level instrument market size exceeded the $5 billion mark in 2023. Among numerous level measurement devices, radar level sensor stand out, leading the market with an average annual growth rate of 8.2%. This non – contact measurement device based on the principle of electromagnetic waves, with its excellent measurement accuracy of up to ±1mm and strong adaptability to operate stably under extreme conditions ranging from – 200°C to + 400°C, is gradually revolutionizing the measurement system of the process industry. The following article will deeply and comprehensively analyze the core technical principles of radar level sensor and explore their unique value in different industrial scenarios.
I. In – depth Analysis of Technical Principles
1.1 Electromagnetic Wave Propagation Theory
The core operation of radar level sensor is based on the electromagnetic wave propagation laws described by Maxwell’s equations. The microwaves emitted by the sensors typically have frequencies of 6GHz, 26GHz, or 80GHz. When these microwaves propagate to the interface between air and a medium, they will be reflected in accordance with Snell’s law. The degree of reflection is mainly determined by the dielectric constant of the medium. Generally, for liquids with a dielectric constant ε_r > 1.4, take crude oil as an example, its dielectric constant ε_r = 2.1. Such liquids can reflect more than 10% of the transmitted power of microwaves. Such a high reflection energy provides a solid guarantee for reliable detection, enabling the sensor to accurately capture the reflected signal and laying the foundation for subsequent measurement work.
1.2 Time – Domain Reflectometry (TDR)
Pulse – type radars adopt advanced nanosecond – level ultra – short pulse (<1ns) technology. It calculates the distance between the sensor and the measured object by accurately measuring the time difference ΔT between the transmitted wave and the received echo. The calculation formula is D = c×ΔT/(2√ε_r), where c is the propagation speed of electromagnetic waves in a vacuum. For example, the 80GHz high – frequency sensor developed by the German company VEGA has an extremely high time resolution of up to 3.3ps. This excellent performance enables its distance resolution to reach 0.5mm. With such high precision, it can achieve millimeter – level accuracy in liquid – level measurement in scenarios with strict requirements for measurement accuracy, such as LNG storage tanks, effectively meeting the needs of high – precision measurement in industrial production.
1.3 Frequency – Modulated Continuous Wave (FMCW) Technology
FMCW – type sensors use linear frequency – modulation technology. Take the case of the 26GHz frequency band with a 2GHz bandwidth. It generates a signal with a continuously changing frequency. The frequency difference Δf between the received echo and the transmitted wave has a linear relationship with the liquid – level distance. The specific formula is Δf = (B×2D)/(c×T_m), where B represents the bandwidth and T_m is the modulation period. One of the significant advantages of this technology is its strong anti – interference ability. In a strong – interference environment, its signal – to – noise ratio can reach more than 80dB. This enables it to still measure the liquid level stably and accurately in complex environments such as industrial sites with a large amount of electromagnetic interference.
1.4 Signal Processing Innovation
Modern radar level sensor integrate DSP digital signal processors and adopt multiple echo tracking algorithms (MET) and adaptive filtering technology. The 5708 series of products from American company Rosemount is a typical example. This series of products can accurately identify the true liquid surface even when the foam layer thickness reaches 2 meters through FFT spectrum analysis technology. After actual testing, its misjudgment rate is lower than 0.01%, greatly improving the accuracy and reliability of measurement and effectively avoiding measurement errors caused by foam interference.
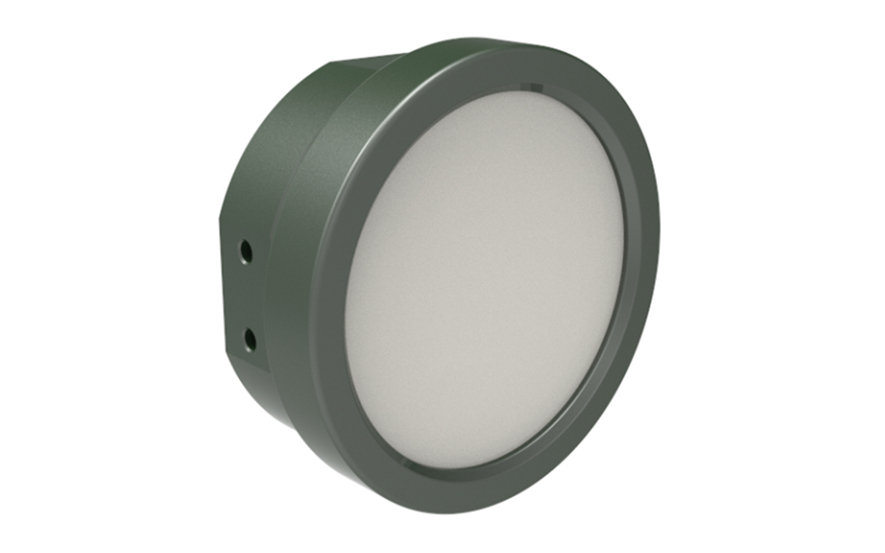
II. Product Types and Technological Evolution